Process intensification: The key to sustainability in chemical engineering
May 13, 2024
By Chris Cogswell, PhD
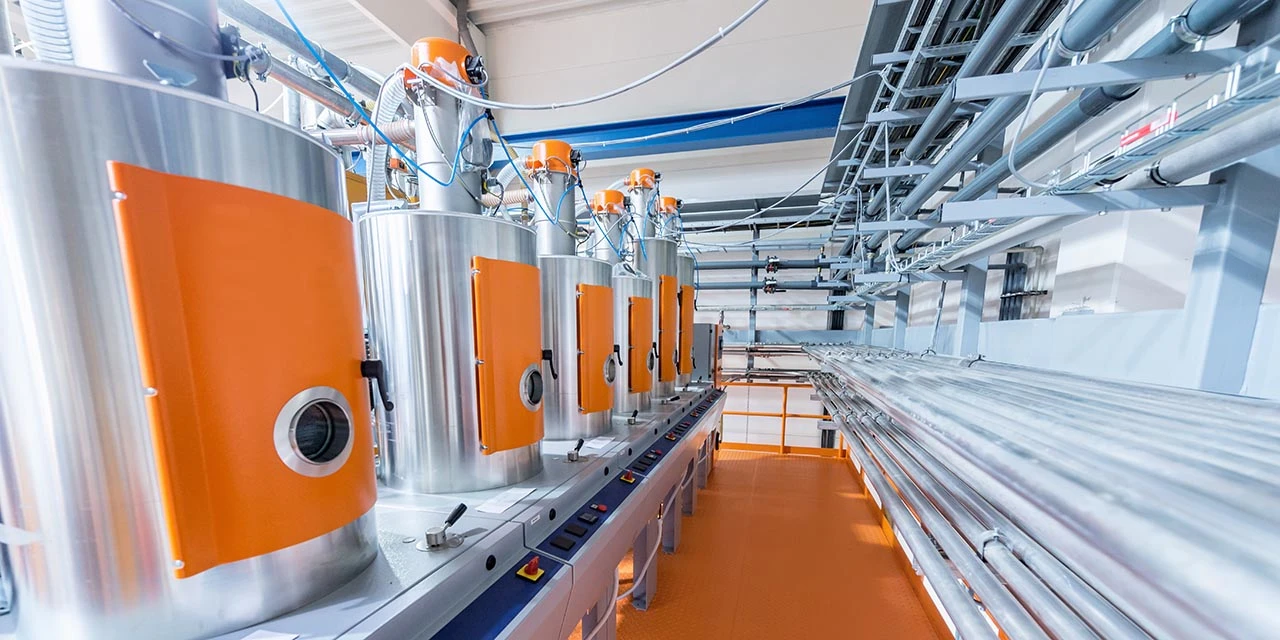
Photo © istock.com/yoh4nn
Learn more about this vital concept in chemical engineering, how it supports the UN’s sustainability goals and how it’s being applied by industry leaders
Innovation is the key to sustainability. To reach sustainability targets, the chemical industry must embrace sustainable processing and energy-efficient technology, driving industry improvements through novel tools and techniques. That’s the topic of a new webinar.
Sustainable innovation in chemicals: Mastering process intensificationopens in new tab/window is the fourth webinar in the series Sustainability in action: Real-world examples for a greener future. In this episode, Jan Harmsenopens in new tab/window, a pioneer in process intensification and former engineer at Shell, shares his experience in the industry.
A key takeaway? “Engineers play a key role in getting the sustainable development goals into actual practice,” Harmsen says.
The implementation of process-intensified equipment and methods in the chemical industry holds significant promise in addressing critical facets of energy, sustainable consumption and production, and climate action.

Jan Harmsen
What is process intensification?
In his book Process Intensification — Breakthrough in Design, Industrial Innovation Practices, and Educationopens in new tab/window, Harmsen defines process intensification as:
A set of radically innovative process-design principles which can bring significant benefits in terms of efficiency, cost, product quality, safety and health over conventional process designs based on unit operations.
It’s based on four principles outlined by Van Gerven and Stankiewicz in The Fundamentals of Process Intensificationopens in new tab/window:
Maximize the effectiveness of molecular events: altering the reaction rate by managing the frequency, energy, and timing of molecular collisions.
Ensure each molecule has a uniform experience: reducing velocity, temperature, and concentration differences across a process.
Optimize driving forces and specific surface areas: achieving high heat and mass transfer rates by maximizing the driving force and specific surface area needed for these processes.
Maximize synergistic effects of partial processes: leveraging the synergy between phenomena and operations within a single equipment.
While not entirely novel to chemical engineering, these principles become explicit objectives through intensified processes. A fully intensified process embodies all these principles by applying fundamental PI approachesopens in new tab/window across four domains:
Spatial (structure)
Thermodynamic (energy)
Functional (synergy)
Temporal (time)
The primary focus when considering process intensification solutions has been on process improvement through continuous processes. This focus stems from the understanding that transitioning from batch to continuous operation inherently results in more condensed, energy-efficient processes.

Source: Enrique A. López-Guajardo et. al.: Process intensification 4.0: A new approach for attaining new, sustainable and circular processes enabled by machine learningopens in new tab/window, Chemical Engineering and Processing — Process Intensification (October 2022)
Eastman Chemical Company’sopens in new tab/window methyl acetate production via a reactive distillation column is a classic example of process intensification. “There was an enormously clever project run by Eastman Chemical where they reduced 11 process steps into one column,” Harmsen says. “And if you look at this historic case of process intensification, it was far more reliable to scale.”
Process intensification’s role in meeting sustainability goals
PI principles align with several sustainability objectives outlined by the United Nations’ Sustainable Development Goals (SDGs)opens in new tab/window encompassing energy efficiency, waste reduction, resource conservation, emission reduction, circular economy principles and sustainable development.
Goal 6: Access to clean water and sanitation for all
Water scarcity is a major global concern. Estimates show that water demand in manufacturing is expected to increase by 400%opens in new tab/window over the next 25 years. In Europe alone, the chemical and refinement industry is responsible for 50% of all water useopens in new tab/window in the manufacturing industry. Process intensification can significantly reduce water waste and improve water management in chemical processing through innovations like closed-loop systems, membrane filtration, and water recycling.opens in new tab/window
Goal 7: Affordable and clean energy
Process intensification contributes to Goal 7 by decreasing energy consumption in chemical processes and encouraging increased utilization of renewable energy sources. An example of this in action is a recent study of process intensification methods in dimethyl carbonate production, which found that hybrid heat integration resulted in 38.33% energy savingsopens in new tab/window compared to conventional pressure-swing separation designs. Reduced generation of unwanted byproducts, compact equipment design, continuous processing, and accelerated reaction rates all play roles in achieving these energy savings.
Goal 9: Infrastructure and industrialization
Innovation, sustainable industrial processes and resilient infrastructure naturally emerge by adopting PI. This approach enables the chemical process industry to modernize outdated and inefficient industrial infrastructure, promoting sustainability and resource efficiency in manufacturing. For instance, implementing multifunctional reactors consolidates multiple process steps into a single chamber, reducing overall utility requirements and creating energy savings.
Goal 12: Responsible consumption and production
Process intensification supports the advancement of environmentally responsible chemical management by enhancing process safety and minimizing waste generation. For example, continuous processing reduces waste and byproduct generation, decreases energy and water consumption and helps curb emissions leading to more environmentally responsible production of chemicals.
Goal 13: Climate action
As the global community strives to mitigate the impacts of climate change, PI plays a pivotal role by accelerating the use of renewable energy into existing chemical plants, creating compact and efficient processing equipment, and reducing water and energy usage. For example, electrochemical reactors or electrically heated micro-reactors can transform heavy greenhouse gas emitters into leaders in green chemistry.
Industry applications: Process intensification solutions
As industries seek innovative solutions to optimize operations, several companies have emerged as leaders in building process intensification solutions.
Synthio Chemicals
Synthio Chemicalsopens in new tab/window is a chemical manufacturing and engineering services firm that bills itself as “chemistry for the new millennium.” Founded in 2017, the company provides process intensification solutions for industrial-scale chemical production. According to Synthio Chemicals, what differentiates it from conventional processes is its “proprietary continuous-flow production platform,” which rapidly and safely produces challenging or costly chemicals at scale.
Chemtrix
Established in 2008, Chemtrixopens in new tab/window works with manufacturers in the fine chemical and pharmaceutical industries to create user-friendly and scalable reactors. Through this work, Chemtrix has designed a range of continuous Flow Reactorsopens in new tab/window suitable for chemical processes ranging from screening reactions at milligram-scale to large-scale industrial production.
CoorsTek
An active leader in the industry since 1910, CoorsTekopens in new tab/window manufactures a wide range of technical ceramics for various industries, including chemicals, medical, and energy. One key feature is a novel process that uses an advanced ceramic membraneopens in new tab/window to “make the direct, non-oxidative conversion of gas to liquids for the first time.” According to CoorsTek, this process reduces costs, consolidates multi-step processes and eliminates CO2 emissions.
NiTech Solutions
NiTech Solutionsopens in new tab/window considers itself “one of the world’s leading authorities on the use of continuous baffled reactor and crystallization technology.” Its innovative continuous flow reactor technology promises to deliver savings and limit harmful emissions. The company offers equipment on any scale, from laboratory to pilot to commercial.
Gain deeper insight into process intensification with Elsevier
Watch the webinar Sustainable innovation in chemicals: Mastering process intensificationopens in new tab/window to:
Gain valuable insights from Jan Harmsen’s wealth of expertise in green chemistry and process design.
Explore advanced process intensification design techniques and how to leverage them for commercial success and enhanced efficiency.
Take a practical look into sustainable engineering principles through past and current applications in the industry.
Watch previous Sustainability in Action webinars
Stay tuned for future webinars in the Sustainability in action series.
Read related stories
Contributor

CCP
Chris Cogswell, PhD
Customer and Engineering Global Consultant
Elsevier
Read more about Chris Cogswell, PhD